“I will always push to have ATSPACE on my future projects which is no small part due to your team and especially to Keith. Hope to work with you in the future.”
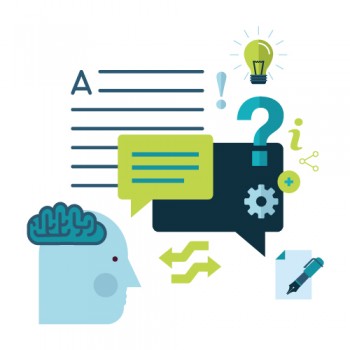
Your questions answered
Click on a category below to find answers to the most common questions we’re asked. If you want to find out more please contact us.
- BREEAM
- Home Quality Mark – NEW
- Code for Sustainable Homes
- Commercial Air Testing
- Daylight Calculations
- Display Energy Certificate
- Energy Statement
- Passive House
- Residential Air Testing
- SAP/EPC
- SAP/EPC for Extensions
- SAP/EPC for Conversions
- SBEM/EPC
- Acoustic Services
- Thermography
- Ventilation – Part F
- Water Calculations
- Terms and Conditions
What is BREEAM all about?
BREEAM is the Building Research Establishment Environmental Assessment Method for buildings and large scale developments – such as student & sheltered living accommodation, as well as non-dwellings such as offices, schools and commercial premises.
BREEAM sets the standard for best practice in sustainable building design, construction and operation and is recognised as one of the most comprehensive measures of a building’s environmental performance.
Within the UK, BREEAM also has standard schemes that have been tailored for such developments as hospitals, prisons and other non-standard building types.
Are there regulations for BREEAM?
Whilst the BREEAM standard is voluntary – some local authorities and developments funded by such organisations as the Housing & Communities Agency could set sustainability targets as a planning condition which could have a BREEAM requirement.
What does BREEAM entail?
Under the BREEAM process, our certified BREEAM Assessor will review your proposed development and award ‘Credits’ that the Project Team agrees to demonstrate compliance with 10 Categories. These ‘Credits’ are then weighted and combined to calculate an overall score – such that the proposed building will be rated on a scale from ‘PASS’ through to ‘OUTSTANDING’.
BREEAM requires a 3-stage process to be carried out:
• Pre-Assessment – Initial Discussions + Advice & Guidance ⇒ Agreed ‘Action Plan’
• Design Stage – Drawings Review + Assessment of Development + Assign Credits ⇒ Interim Report
• ‘As Built’ Review – On-site Review + Review Evidence of Construction & Commitments made ⇒ Final Report for submission to the BRE
What does a BREEAM assessment take into consideration?
Under the BREEAM process, our certified BREEAM assessor will review your proposed development and award ‘Credits’ that the Project Team agrees to demonstrate compliance with:
• Management – effectiveness of the building operation
• Health & Wellbeing – level of occupant control over heating, lighting, air quality and noise
• Energy – level of energy efficiency and CO₂ emissions
• Transport – effectiveness of site provisions to reduce transport related CO₂ emission levels
• Water – level of buildings water efficiency
• Material – types of materials utilised and responsibility of sourcing practices
• Waste – reduction of waste generated during construction & operation of the building
• Land Use & Ecology – consideration of location and associated impacts
• Pollution – level and type of emissions by the building
• Innovation – reward of innovation in the pursuit of environmental performance
When is the best time to start planning BREEAM?
ATSPACE recommend that you appoint a BREEAM Assessor during the early design stages of the project – as this will make it easier to achieve the desired rating cost effectively – and often with a cost saving.
By appointing a BREEAM Assessor later in the overall process may result in the desired rating being unobtainable or only achievable through additional investment and, additionally – certain aspects within the BREEAM process need to be carried out very early on concept design phase e.g. feasibility study into low to zero carbon technologies.
What does BREEAM provide?
BREEAM is used by a wide range of professionals – from Planners & Development Agencies through to Design Teams and Property Agents, and provides:
• Market recognition for low environmental impact buildings
• Confidence that proven environmental practice is incorporated into the building
• Inspiration to find innovative solutions that minimise environmental impact
• A benchmark that is higher than the regulation standard
• A system to reduce running costs and improve working & living environments
• A standard demonstrating progress towards corporate & organisational environmental objectives
What are BREEAM ‘Weightings’ and BREEAM ‘Score’?
How can ATSPACE help?
ATSPACE offer our clients a 3-stage process for BREEAM and we recommend that an assessor is appointed at the earliest opportunity in the project – as this will help in achieving the desired BREEAM rating in the most cost-effective manner.
STAGE 1 – BREEAM pre-assessment
During the first stage of the BREEAM assessment process, our accredited assessor will meet with the project team to:
• Provide advice and an initial view on the sustainability of the proposed development
• Advise on elements that require inclusion in the detailed design planning phase
• Respond to queries from the project team
• Agree an action plan – documenting what is required to achieve the desired BREEAM rating.
STAGE 2 – BREEAM design stage assessment
Once the detailed drawings and specifications have been completed, our assessor will meet up again to:
• Assess the building against the BREEAM scheme’s credit criteria
• Assign credits based upon information and evidence supplied by the project team
• Produce an interim report which is issued to the BRE (Building Research Establishment).
STAGE 3 – BREEAM post-construction review
Upon completion of the development – our assessor will conduct a full on-site visit to:
• Ensure the construction meets commitments made at the design stage with evidence from the project team
• Produce the final BREEAM assessment report and arrange for submission to the BRE.
What other services do I need to consider in relation to BREEAM?
Design Stage
Drawing Review / Advice & Guidance
SBEM Calculations
Construction Phase
Pre-Test Inspections
Contracting Services
‘As Built’ Stage
Air Tests & Certification
Thermographic Survey
SBEM Calculations & EPC Smoke Testing
What is Home Quality Mark all about?
The Home Quality Mark (HQM) is a national standard for new homes, developed by the Building Research Establishment (BRE), which uses a simple 5-star rating to enable housing developers to showcase the quality of their projects and to allow potential buyers to not only know the environmental impact, running costs and comfort of the house, but also use this to compare with other properties.
The HQM is part of the BREEAM (Building Research Establishment Environmental Assessment Model) family which set the standard for best practice in sustainable building design, construction and operation and is recognised as one of the most comprehensive measures of a building’s environmental performance.
Within the UK, BREEAM also has standard schemes that have been tailored for such developments as hospitals, prisons and other non-standard building types.
Are there regulations for Home Quality Mark?
Whilst the HQM standard is voluntary, the use of indicators – based on the key interests of the major participants, such as home occupants, developers and planners – make it a useful tool for assessing whether a development has achieved certain sustainability targets that are often set as planning conditions.
These indicators are based on the perspectives of the participants. For example, indicators from a householder perspective may cover such areas as running costs, positive impact on health and wellbeing and the environmental footprint. Over time, further indicators will be developed from other perspectives, including those of developers, financial institutions, landlords and local authorities.
What does Home Quality Mark entail?
Under the HQM process, our certified HQM Assessor will review your proposed development and award ‘credits’ that the project team agrees to demonstrate compliance with 3 main categories. These credits are then used to calculate an overall score – measured through the use of a 5-star system, and, with different weightings are also used to rate the development against the key indicators.
HQM requires a 3-stage process to be carried out:
• Pre-assessment – initial discussions + advice & guidance ⇒ agreed ‘action plan’
• Design stage – drawings review + assessment of development + assign credits ⇒ interim report
• As built review – on-site review + review evidence of construction & commitments made ⇒ final report for submission to BRE.
What does a Home Quality Mark Assessment take into consideration?
Under the HQM process, our certified HQM Assessor will review your proposed development and award credits that the project team agrees to demonstrate compliance with:
• Knowledge Sharing – This section rewards good processes and solutions which reduce the gap between the designer, constructor and householder. This ensures that the so-called ‘performance gap’ is minimised and that the home is truly capable of ‘doing what it says on the tin’.
• Our Surroundings – This section rewards homes built to work with their surroundings, and with what these may become through changes in population and climate, to maximise benefits and minimise impacts now and into the future.
• My Home – This section rewards homes that are built to ensure that they provide spaces that are healthy to live in, but also don’t cost the earth. ‘My home’ sets specific performance outcomes for your home whilst allowing a degree of flexibility in the means of determining this. Wherever possible, commonly used assessment methodologies will be used, based on simple calculations to avoid additional costs. These will include the use of an extended Building Regulations calculation, Passivhaus certification and more detailed dynamic performance modelling as appropriate to calculate a number of performance characteristics relating to energy, comfort and overheating.
When is the best time to start planning for Home Quality Mark?
ATSPACE recommend that you appoint a HQM Assessor during the early planning stages of the project (RIBA Stage 1 – Preparation and Brief) – as this will make it easier to achieve the desired rating cost effectively – and often with a cost saving.
By appointing a HQM Assessor later in the overall process may result in the desired rating being unobtainable or only achievable through extra investment and, additionally, certain aspects within the HQM process need to be carried out very early on in order for credits to be awarded, e.g. A Security Needs Assessment must be completed by a Suitably Qualified Security Specialist by the end of RIBA stage 2 – Concept Design – in order to allow the awarding of credits in most cases.
What does Home Quality Mark provide?
HQM can be used by a wide range of professionals – from planners and development agencies through to design teams and property agents, and provides:
• Market recognition for low environmental impact buildings
• Confidence that proven environmental practice is incorporated into the building
• Inspiration to find innovative solutions that minimise environmental impact
• A benchmark that is higher than the regulation standard
• A system to reduce running costs and improve working & living environments
• A standard demonstrating progress towards corporate & organisational environmental objectives.
What are Home Quality Mark ‘Indicators’ and Home Quality Mark ‘Score’?
The HQM Assessor takes into account a wide range of ‘assessment issues’ that correspond to an agreed number of total available credits. The number of credits achieved for each assessed issue are then counted to give an overall score – out of 500 total:
How the indicator scores are calculated
Each assessment issue is also given a score for each of the 3 indicators, depending on the issues relative contribution to meeting the indicators:
The number of credits achieved for each issue is multiplied by their weighting for each indicator and the total scores towards each are calculated as follows:
How can ATSPACE help?
ATSPACE offer our clients a 3-Stage Process for HQM and we recommend that an assessor is appointed at the earliest opportunity in the project, as this will help in achieving the desired HQM rating in the most cost-effective manner.
STAGE 1 – HQM Pre-Assessment:
During the first stage of the HQM Assessment process, our accredited assessor will meet with the project team to:
• Provide advice and an initial view on the sustainability of the proposed development
• Advise on elements that require inclusion in the detailed design planning phase
• Respond to queries from the project team
• Agree an ‘action plan’ – documenting what is required to achieve the desired HQM rating.
STAGE 2 – HQM Design Stage assessment:
Once the detailed drawings and specifications have been completed, our assessor will:
• Assess the building against the HQM scheme’s credit criteria
• Assign ‘credits’ based upon information and evidence supplied by the project team
• Produce an ‘interim report’ calculating the potential rating to be achieved if all agreed criteria are met.
STAGE 3 – HQM Post-Construction Review
Upon completion of the development our assessor will conduct a full on-site visit to:
• Ensure the construction meets commitments made at the design stage with evidence from the project team
• Produce the final HQM assessment report and arrange for submission to the BRE.
What other services do I need to consider in relation to BREEAM?
Design Stage
Drawing Review / Advice & Guidance
SAP Calculations + PEA
Daylight Calculations
Construction Phase
Pre-Test Inspections
‘As Built’ Stage
Residential Air Tests & Certification
Thermographic Survey
Sound Insulation Testing
What is the Code for Sustainable Homes all about?
The Code for Sustainable Homes (CSH) is an environmental assessment rating method for new homes which assesses environmental performance in a two-stage process using objective criteria and verification. The results of the Code assessment are recorded on a certificate assigned to the dwelling.
Introduced in 2008 and similar to BREEAM (for non-domestic properties), the CSH is now the national standard for the sustainable design and construction of new homes – with the aim of reducing carbon emissions and to promote higher standards of sustainable design – and covers performance in 9 major areas of environmental impact:
• Ecology
• Energy & CO₂ emissions
• Health & well being
• Management
• Materials
• Pollution
• Surface water run-off
• Waste
• Water
The Code uses a rating system of 1 to 6 levels – with Code Level 6 being the top rating and classified as a zero-carbon home.
How does the Code work?
The Code assesses a new dwelling against nine categories – each of which is allocated a number of credits and associated weighting factor:
When carrying out a CSH Assessment the detailed plans, drawings and building specifications are reviewed and points awarded, based on a percentage system to achieve a Code Level Rating of 1 to 6:
Is the Code for Sustainable Homes mandatory?
Mandatory minimum performance standards are set for some issues. For 3 of these, a single mandatory requirement is set – which must be met, whatever Code Level Rating is sought. Credits are not awarded for these issues and confirmation that the performance requirements have been met is a minimum entry requirement for a Level 1 rating. These 3 uncredited issues are:
• Environmental impact of materials
• Management of surface water run-off from developments
• Storage of non-recyclable waste and recyclable household waste
In addition, many local authorities are increasingly making the following 2 issues mandatory:-
• Dwelling Emission Rate (DER) – The SAP Calculations will determine the Target Emission Rate (TER) for the dwelling and the DER is calculated during the preparation of the as-built SAP and local authorities have laid down minimum standards for CO₂ emissions:
• Indoor Water Usage – Determined during the development of Part G Water Calculations and must not exceed a water consumption rate of over 120 litres per person per day.
What are the regulations for Code for Sustainable Homes?
Download the Code for Sustainable Homes Technical Guide
When is the CSH Assessment carried out?
The CSH Assessment is carried out in 2 distinct stages:
• Design stage – the aim of this stage is to:
– Assess the design specifications before construction begins for each individual dwelling, to determine the design stage or interim rating
– Award (subject to quality assurance) a design stage or interim certificate
• Post construction stage assessment – the aim of this stage is to:
– Assess each dwelling as-built to determine the final score and code level for the dwelling
Within the post construction Assessment, the assessor will confirm that the dwellings have been built to the specifications laid down in the design stage assessment. The assessor will also note that if there are any variations, that they have been documented and reassessed and a new score and code level is calculated.
Does CSH take into account Sound Insulation?
The CSH offers credits awards for achieving greater standards of sound insulation than the Building Regulations currently require – which means that up to four extra credits may be gained from upgrading separating wall/floor specifications.
To achieve the maximum four credits the separating floors and walls have to be shown to achieve 8dB above the performance requirements of PART E of the Building Regulations. The level of compliance must be demonstrated and proven through a Pre-Completion Sound Test.
How can ATSPACE help?
ATSPACE offer our clients a full CSH Assessment service at both design stage and post construction stage. We recommend that an assessor is appointed at the earliest opportunity in the project as this will help immensely in fully understanding the implications of the Code for Sustainable Homes and what is required to achieve the desired rating at the end of construction.
During the design stage we will provide advice and guidance, not only regarding heating systems, insulation, air tightness, ventilation & lighting, but also provide advice in areas related to CSH, including: bicycle storage, greywater recycling and office provision & white goods – and how these can help boost your overall points score!
Because we offer clients a full building compliance service, from SAP Calculations through to Air Testing, we would be happy to offer clients who are looking achieve CSH status, a fully integrated service for design stage through to post construction certification.
What other services do I need to consider in relation to Code for Sustainable Homes?
Design Stage
Drawing Review / Advice & Guidance
Sound & Acoustics Design
SAP Calculations & PEA
Construction Phase
Pre-test Inspections
Per-Completion Air Tests
Contracting Services
As-built Stage
Air Tests & Certification
Pre-Completion Sound Tests
SAP Calculations & EPC Water Calcs. – Part G
Ventilation Part F
What is Commercial Air Testing all about?
Air leakage is one of the major components affecting overall energy consumption within buildings and the UK government has a long-term goal of achieving a 60% reduction in UK CO₂ emissions by 2050.
Hence, in order to comply with Part L2A & L2B of the Building Regulations, all commercial and public buildings over 500m² are required to have successfully passed a Commercial Air Pressure Test as part of the building compliance process.
Over the past 10 years, here at ATSPACE, we have successfully undertaken many hundreds of Commercial Air Pressure Tests in schools, offices, superstores, public buildings and even prisons, including:
• Large Superstores – for Tescos & Lidl
• UK’s 1st. Passive House Care Home – in Brackley, Northants
• Natural History Museum – London
What are the regulations for Commercial Air Leakage Testing?
Part L2A of the Building Regulations details the requirements for new build commercial premises. Part L2B of the Building Regulations covers those requirements that are necessary for conversions and extensions.
Approved document L2A of the 2006 Building Regulations requires all commercial and industrial buildings with a gross floor area in excess of 500M² – to be tested for air permeability to meet a minimum standard of 10m³ /(h.m² ) at 50 Pa. (I.e. An air leakage rate of ≤ 10 cubic metres per hour, per metre squared at a pressure of 50 pascals).
However, in the drive towards increased energy efficiency and increased comfort for the building’s occupants – a level of 3m³ /(h.m² ) has often been set for air-conditioned buildings and in some of the large superstores we have tested – the developers have set even tighter standards to achieve levels as low as 2m³ /(h.m²).
What are the common areas of air leakage?
Achieving a high degree of air tightness is a vital component of sustainable design and ultimately – reduced energy costs. Hence, in order for mechanical ventilation air conditioning and heating systems to operate at optimum efficiency and to avoid draughty conditions within the building – areas of ‘air leakage’ should be identified and minimised throughout the design and build processes.
Within commercial buildings – common areas where ‘air leakage’ can occur include:
• Pipework
• Ceilings
• Dry lining systems
• Windows and door frames
• Riser shafts
• Loading bay doors
• Steelwork penetrations
• Curtain walling systems
• Electrical services
Please download our FREE Hints and Tips Guide which will help you identify the most common areas where air leakage can occur so that you minimise the need for any remedial action.
How can ATSPACE help?
At ATSPACE – we have all the skills, experience and appropriate accreditations to provide our clients with a comprehensive ‘building compliance’ package of products and services – to help ensure that your construction projects meet the standards as laid down by the Building Regulations – Part L2.
From initial discussions – regarding drawings and design reviews, SBEM Calculations and Pre-Test Inspections through to the completion of Air Testing & Certification – we will be happy to discuss your requirements, provide you with a detailed project proposal and deliver you a first class professional Service with a best price guarantee.
When do I need to start planning for my Commercial Air Leakage Test?
Planning for a successful Commercial Air Leakage Test – begins at the design stage of your project.
Architects should design-in air tightness as part of their planning process and building contractors and tradesmen should build-in air tightness throughout each phase of construction.
That way you will maximise your chances of success come the final test day!
What do I need to do to prepare for success?
Ideally, a developer should develop an ‘air tightness plan’ – which covers the project from start-to-finish.
This way the individual air tightness requirements for each phase of construction can be communicated, monitored and signed-off upon completion of each phase. By adopting this structured approach from the outset of the project you will maximise your chance of a successful Air Leakage Test – and minimise the cost of remedial action should the test be initially unsuccessful.
To help you prepare and to ensure the environment is fully ready for the Air Testing to take place – please download our FREE ATSPACE Commercial Air Test Preparation Checklist
What information will ATSPACE require before the Air Test?
The key information we require is the envelope area (M² of floors, walls & ceiling areas) – together with the proposed Target Emission Rate (TER) for the building – as these are key pieces of data used in calculating the Air Permeability Rate during our Air Test procedure.
These pieces of information will be held in the detailed drawings and the SBEM Calculations – so we would appreciate copies prior to the test being carried out – because dependent upon the complexity of the structure, it may take a considerable amount of time to calculate the envelope area on the test day itself.
When will the Commercial Air Test be carried out?
We normally carry out our Air Testing at the end of the construction process – at a date and time to suit you.
Just book your testing slot with our customer services team – who will email you with full details of our engineers arrival time, together with a final a copy of the ATSPACE Commercial Air Test Preparation Checklist so that you can be fully prepared.
Our air test engineers are used to carrying out testing in all types of environment and having discussed the Air Test with your nominated site contact we will carry out the testing with minimum fuss or disruption to other ongoing activities.
What does the test entail?
Once on site, our engineer will initially undertake a walk through the building to determine if all activities on the pre-test checklist have been completed and, unless already supplied, will need to calculate the envelope area of the building (M²) and to log down the target air permeability rate to be achieved.
Depending upon the size of the building our air test engineer will install one or more air-tight screen/s to an agreed entrance door/s to the building – a fan is then mounted into the screen and activated to blow air into or out of the building to create a price differential between inside and outside of approximately 50 Pa (Pascals). Up to 7 readings are taken with a no more than 10pa difference. A mean average is taken to establish the buildings leakage rate @ 50pa.
Additionally, both before and after the test, our engineer will take a number of other readings, including barometric pressure, internal / external temperature and wind speed. Through the use of specialist software and the fan/s in operation, our engineer will be able to fully carry out the test and measure the air permeability rate for the building.
To setup and conduct a single air test will be dependent upon the size of the building and will take approximately 1-3 hours to complete, in which time nobody can be allowed to enter or exit the building during the test itself. Tradesmen or contractors can remain working inside throughout the testing process.
What happens after the test is carried out?
Upon completion of the air test, our engineer will know whether or not the building has met the required standard for achieving a pass and he will then immediately inform the site contact of the outcome.
Under normal circumstances, the engineer will then upload the respective test results to our in-house systems, the client will then be invoiced the next working day and test reports and certificates issued upon receipt of payment for test.
By prior arrangement, we are also able to issue test reports and certificates on a same day basis, via email, should the client require immediate access to the results.
What happens if the building fails the air test?
At ATSPACE our objective is to help you achieve a pass, which is why we offer clients a full range of support services to help you achieve success. However, in the unlikely event of a test failure there are a number of options that can be carried out to detect any areas of air leakage – including:
• Smoke testing – where we can use a combination of smoke and/or smoke pencils to identify leakage points from the building
• Thermography – through the use of infra-red cameras to identify hot/cold spots and hence, areas of air leakage.
However, if you have planned to achieve a successful Commercial Air Test from the start of your project – designed-in air tightness within the building fabrication and built-in air sealing during the construction process – then the chances of failure are greatly reduced.
What other services do I need to consider in relation to Commercial Air Testing?
Design Stage
Drawing Review / Advice & Guidance
SBEM Calculations
Construction Phase
Pre-Test Inspections
Contracting Services
‘As Built’ Stage
Air Tests & Certification
Thermographic Survey
SBEM Calculations & EPC Smoke Testing
What are Daylight Calculations all about?
Part L of the Building Regulations places responsibility upon the designer to maximise the use of natural daylight, whilst achieving a balance between adequate light levels and controlling solar heat gain – and many councils are now requiring that light issues are addressed as part of a planning application.
ATSPACE are able to assist in providing advice and guidance and the preparation of Daylight Calculations to provide the required evidence and reports which will show if neighbouring properties are adversely affected by a new development, extension or wall to assist with gaining planning approval.
When do I need Daylight Calculations?
Over recent years there has been a significant increase in the importance of environmental concerns – and – local councils continue to place greater significance on considering the effect that proposed developments will have on the daylight and sunlight levels received by neighbouring properties.
For this reason, many local authorities now require daylight and solar shading calculations and ‘right of light’ assessments to be submitted in support of planning applications – and ATSPACE will provide you with the services of a fully certified assessor to evaluate the daylight efficiency of your project and produce the necessary evidence and reports to support your planning application.
Furthermore, measuring daylight efficiency is part of the requirement for both BREEAM and the Code for Sustainable Homes – and the data from daylight calculations can be used to obtain appropriate ‘credits’ at appraisal time.
What are the regulations for Daylight Calculations?
New buildings need to ensure that they do not reduce daylight levels in neighbouring buildings to an unacceptable degree. As a rule of thumb for residential buildings this will require at least 12 metres clearance between the primary windows of habitable rooms and adjoining buildings to retain adequate day lighting.
Natural daylight has a clear positive influence on people’s wellbeing. The living or working environment is more comfortable when illuminated naturally as it provides a better quality of light and the required minimum daylighting standards for new buildings are set out in BS 8206-2. Given this standard – Local Authorities are increasingly requesting these specialist reports in support of planning applications.
Click HERE – to Download – BRE Report – Planning for Daylight & Sunlight – Guide to Good Practice
How can ATSPACE help?
If your local council requires submission of Daylight Calculations, then our fully accredited assessors are here to help and through the use of certified modelling software, our assessors our able to:
• Evaluate the proposed building in depth
• Assess the impact upon neighbouring properties
• Determine the impact of solar energy upon the building
• Recommend effective balance between natural and artificial light
• Identify optimum sizing and positioning of glazing within the building
• Determine the maximum envelope area of the new development
At ATSPACE, we pride ourselves in being able to provide our clients with a complete package of building compliance services from initial advice and guidance, through successful planning application at design stage, and ultimately full building control sign-off at the ‘As Built Stage’ – all focussed upon ensuring the your development project becomes a resounding success.
What is a Display Energy Certificate?
A Display Energy Certificate (DEC) shows the energy performance of a building – based upon actual energy consumption. The DEC provides an energy rating for the building on a scale of A to G, where A is the lowest level of CO₂ emissions and G is the highest level of CO₂ emissions.
DEC’s for buildings over 1,000m² also show the operational ratings for the previous 2 years. The operational rating is based on the actual amount of energy used (from meter readings) and the various types of energy consumption are brought together on a common basis – which is recorded as CO₂ emissions.
Why is a Display Energy Certificate required?
The purpose of introducing DEC’s is to raise public awareness of energy use and to inform visitors to public buildings about the actual energy usage of the building that they are visiting.
All DEC’s must be displayed in a prominent place that is clearly visible to the visiting public and the organisation must also have access to a valid advisory report which contains recommendations for improving performance within the building.
What type of buildings require a Display Energy Certificate?
DEC’s and accompanying Advisory Reports are required on all buildings with a total useful floor are in excess of 500m² that are occupied by public authorities and visited by the public.
For the purposes of the regulations, a building is described as a roofed construction having walls, for which energy is used to condition the indoor climate, and a reference to a building includes a reference to a part of the building which has been designed or altered to be used separately.
From July 2015, these regulations have been further extended and DEC’s will be required to be displayed for all such buildings that are in excess of 250m².
What is an Advisory Report?
The Advisory Report contains recommendations for possible improvements regarding energy consumption within the building, including low-cost operational and management improvements, improvements to the building fabric or services and opportunities for the installation of Low and Zero Carbon (LZC) technologies.
The report enables the occupier to identify what may be done to improve building energy management, building services, and therefore reduce energy consumption and CO₂ emissions.
The advisory report lists the recommendations by payback period as follows:
• Short-term – Up to 3 years – e.g. building energy management measures
• Medium-term – 3-7 years – e.g. upgrading building services
• Long-term – More than 7 years – e.g. Low and Zero Carbon (LZC) technologies
Who can produce a Display Energy Certificate?
Under the legislation, an appropriately accredited energy assessor is the only person who can produce a DEC & Advisory Report for your building.
An organisation’s employees are also permitted to produce DEC’s – provided that they have met the standards of and have been accepted by an approved accreditation scheme.
What information is required to produce a Display Energy Certificate?
The building occupier, in collaboration with the energy assessor, will need to obtain actual meter readings or consignment notes for all fuels used in the buildings that are affected by this legislation. This may include gas fuels, oil fuels, solid fuels, district heating and cooling, grid electricity and electricity generated on site or obtained by private distribution systems from other sites.
For district heating and cooling and electricity generated on site, or obtained by private distribution systems from other sites, the average carbon factor for the fuel over the accounting period will need to be obtained e.g. in kg of carbon dioxide per kwh delivered.
You can obtain the information required to produce a DEC from a number of sources:
• on-site energy meters
• building landlord or representatives
• utility suppliers
What is the penalty for not having a Display Energy Certificate?
A local authority can issue a penalty charge notice of £500 for failing to display a DEC at all times in a prominent place clearly visible to the public, and £1,000 for failing to possess or have in their control a valid advisory report.
In addition to these penalties, it will still be necessary to commission the documents, otherwise further offences will be committed. If you can demonstrate that you have taken all reasonable steps to avoid breaching the regulations, then the penalty charge notice must be withdrawn.
If you believe the penalty charge notice should not have been given you can request a review. If you are not satisfied with the outcome of the review you may appeal to the county court within 28 days after you received notice confirming the penalty charge notice.
How can ATSPACE help?
At ATSPACE, our fully qualified energy Assessors follow an established process for providing – advice, guidance, support & certification services – to help ensure that your building fully complies with the up-to-date building regulations regarding Display Energy Certificates & Advisory Reports.
Our aim, at ATSPACE, is to help our customers every step of the way, should you have any queries regarding Display Energy Certificates please give us a call and we will be most happy to help.
What is an Energy Statement?
In addition to a SAP or SBEM Assessment many local authorities are now requiring the provision of an Energy Statement with a planning application – before granting planning permission for building to commence.
As there is currently no national standard format – each Energy Statement that we prepare here at ATSPACE, will be individually created to meet the specific requirements of the local planning authority.
Energy Statements should act as a valuable and accurate working document which sets out the predicted CO₂ emissions and demonstrate potential improvements for reducing energy consumption and emissions – through the use of efficient fabric construction, efficient heating, ventilation and lighting, together with the use of renewable technologies.
When do I need to start preparing my Energy Statement?
The simple answer is at the start of the project! Developing an energy strategy for your proposed development is a key aspect on the journey towards obtaining a successful planning application.
Our experienced energy assessors at ATSPACE will happily meet with your local planning authority to understand their specific requirements to support the planning application – and ultimately prepare the relevant reports to ensure both planning application success, as well as providing your design and construction teams with a valuable working document which can be used throughout the duration of the project.
What is the London Plan?
Whilst there is no national standard for the production of Energy & Sustainability Statements – the Greater London Authority (GLA) has introduced The London Plan and its Policy 5.2 n Plan requires each major development proposal to submit a detailed energy assessment.
The purpose of an energy assessment is to demonstrate that climate change mitigation measures are integral to the scheme’s design and evolution, and that they are appropriate to the context of the development.
The GLA provides guidance for developers and their advisers on preparing energy assessments to accompany strategic planning applications. Each assessment is required to demonstrate how the targets for regulated CO₂ emission reductions will be met using the Mayor’s energy hierarchy – which has applied a 35 per cent carbon reduction target beyond Part L 2013 of the Building Regulations.
Download your copy of the GLA Energy Assessment Guide April 2015
How can ATSPACE help?
To help you meet local requirements for the preparation and delivery of the required Energy Statement our team of ATSPACE assessors will:
• Liaise with the local authority to identify specific requirements
• Carry out a detailed assessment of site conditions
• Recommend the most appropriate technology for generation of renewable energy
• Identify the predicted levels of CO₂ emissions and reduction levels that may be attained
• Compile and submit an energy report to meet local authority planning requirements
The ATSPACE goal is to help all our customers achieve optimum levels of energy efficiency through our comprehensive package of building compliance services including: Air Pressure Testing, SAP & SBEM Calculations and Energy Performance Certificates.
What other services do I need to consider in relation to Energy Statement?
Drawing Review / Advice & Guidance
SAP Calculations & PEA
BREEAM Assessment
Code for Sustainable Homes
What is Passive House (Passivhaus) all about?
Developed in Germany in the 1990’s – The Passivhaus Standard (Passive House) is the fastest growing energy performance standard in the world – and, above all, the standard promotes a robust approach to building design – to create a dwelling that has an excellent thermal performance, coupled with exceptional air tightness and heating which can be recovered and circulated by a Mechanical Ventilation & Heat Recovery (MVHR) Unit.
Essentially, when designing a Passive House the prime objective is to minimise heating and cooling loads as much as possible and develop an airtight building which has a continuous supply of low volume filtered fresh air that provides balanced and controlled ventilation with high-efficiency heat exchange. Passive Houses are exceptionally comfortable, healthy and affordable to occupy – yet there are no prescriptive construction methods, thereby leaving the appearance of the Passive House to be determined by the client and architects.
What are the key attributes of a Passive House?
The key attributes of the Passive house standard centre around achieving maximum levels of energy efficiency through:
• Super insulation – ensuring excellent heat retention within the building
• Excellent draught proofing – the house has so few gaps and holes that almost no air can enter the building other than through the carefully controlled MVHR unit
• Passive solar gain – carefully placed windows mean the sun will warm the building naturally
• Low energy appliances – the most energy efficient appliances can dramatically help you reduce your energy consumption
• Renewable energy sources – using solar PV and thermal, wind or other renewable sources allows you to be even more energy independent
Why does the building need to be airtight?
Achieving a good level of air tightness is vital for achieving optimum levels of energy efficiency – the more cracks and gaps – the draughtier the building, which will in turn lead to increased energy costs caused through this uncontrolled flow of air. To achieve the Passive House standard – one of the key aims will be to create an airtight building which will eliminate draughts, reduce energy consumption and lessen external noise levels.
Within a Passive House – the building has consistent interior surface temperatures and a stable indoor climate – thereby eliminating temperature fluctuations and draughts. However, ample fresh air is supplied at room temperature via high efficiency ventilation such as MVHR systems.
What are MVHR Systems?
MVHR is Mechanical Ventilation Heat Recovery. Having created an airtight building to prevent heat loss, it is equally important to ensure a controlled air flow remains within the building to prevent the air becoming stale or humid.
MVHR Systems are designed to deliver fresh air throughout the building in a controlled manner. The system uses the heat from the exiting environment to heat the incoming fresh air. This not only provides ventilation but also filters out dust particles and balances humidity levels.
What are the benefits of a Passive House?
There are many benefits to a Passive House, including:
• Low energy costs – a Passive House uses very little energy and annual costs are often less than 10% of what a conventional build would cost
• Reliability – the Passive House standard is tried and tested worldwide with tens of thousands of Passive Houses having been constructed. Hundreds of these have been continually monitored and tested with consistently positive results.
• Low running costs – the initial investment costs for a Passive House are slightly higher than a conventional building due to the increased levels of planning and the requirement for superior building components. However, this pays off quickly due to the extremely low running costs and the owner is left with a higher quality building that costs significantly less to run.
• Comfortable living environment – the Passive House environment provides occupants with optimum levels of warmth, humidity, noise and dust.
How can ATSPACE help?
Here at ATSPACE our team of Air Test engineers are familiar with carrying out air leakage testing on Passive House buildings – including: Membrane Testing, 1st FIX Stage Testing and On-Completion Testing to achieve the Passive House standard of ≤ 0.6 ACH.
Such is the experience of our BINDT-certified engineers – we were commissioned to undertake all the required Air Leakage Testing for the first Passive House Care Home to be built in the UK at Juniper House, Brackley. We were also delighted to be invited to check the performance of the first affordable and social housing development built to Passive House standards in Wimbish near Saffron Walden, following installation changes post completion.
What other services do I need to consider in relation to Passive House?
Design Stage
Drawing Review / Advice & Guidance
SAP Calculations & PEA
Construction Phase
Pre-test Inspections & Air Testing
Contracting Services
As Built Stage
Air Tests & Certification
SAP Calculations & EPC
Smoke Testing
What is Air Pressure Testing all about?
Air Pressure Testing (also known as – Air Leakage, Air Permeability or Air Tightness) is the testing methodology used to determine the resistance of the building envelope to inward or outward air leakage, which occurs through gaps, cracks and holes in the fabric of the building.
Achieving a good level of air tightness is vital for achieving optimum levels of energy efficiency – the more cracks and gaps – the draughtier the building – which can lead to increased energy costs.
What are the common areas of air leakage?
Whilst you may have installed excellent insulation and energy efficient heating systems – much of the benefits may be lost unless you pay particular attention to sealing potential air leakage cracks and gaps in such places as:
• around service penetrations (e.g. pipe work and cabling) including those enclosed or boxed-in
• behind fitted units, bath and shower tray panels, toilet units
• at the junctions of external walls and floors, including skirting boards
• around windows and doors, generally at the junction of the frame and the recess
• electricity socket points and light fittings
Please download our free Air Permeability Checklist written in an easy-to-read style and containing all the information you require to plan and prepare your development ready for Air Testing success.
Why do I need to have an Air Pressure Test carried out?
The UK Building Regulations Part L now require minimum standards of air tightness to be achieved in newly constructed buildings and dwellings.
All new buildings and dwellings need to demonstrate a minimum level of air permeability (10m³/(h.m²)) – in the majority of cases this is done through an on-site pre-completion test and the presentation of a PASS test certificate – following tests carried out by an appropriately certified air test engineer.
When do I need to start planning Air Leakage Testing?
During the design stage for your project a SAP Calculation will need to be prepared and submitted to local Building Control before the construction phase can begin. One part of the SAP Calculation will be to determine the Air Permeability Rate (APR) that must be achieved during the final Air Test itself.
In essence, the lower the APR – the more stringent you will need to be during the construction phase in minimising air leakage points throughout the building. At ATSPACE, our building compliance team look at the overall end-to-end process. Our SAP Assessors and Air Test engineers will always try to ensure that the client has a realistic target to hit come the Air Test day itself. Furthermore, ATPACE offers customers a discounted Air Test fee when we have undertaken the SAP Calculations on their behalf.
Therefore, it is vitally important to start planning for air tightness from the outset of your project and to ensure that you develop an air tightness strategy that can be communicated to the contractors and tradesmen during the construction phase of the project.
By adopting a focused approach towards air tightness you will almost certainly obtain a successful pass in the Air Test itself and, more importantly, ensure that long-term energy efficiency savings are achieved. As further insurance ATSPACE will always be happy to provide you with a drawing review and Pre-Test Inspection before all areas are covered at the second fix stage.
When will the Air Leakage Test be carried out?
We normally carry out our Air Testing at the end of the construction process at a date and time to suit you.
Just book your testing slot with our customer services team who will email you with full details of our engineer’s arrival time, together with a final pre-test checklist so that you can be fully prepared. Our Air Test engineers are used to carrying out testing in all types of environment and having discussed the Air Test with your nominated site contact, we will carry out the testing with minimum fuss or disruption to other ongoing activities.
What does the test entail?
Once on site, our Engineer will initially undertake a walk through of the property to determine if all activities on the pre-test checklist have been completed – e.g. trickle vents closed and sealed; extract vents sealed and water traps sealed or filled. Unless already supplied, we will need to calculate the envelope area of the building (m²) and to log down the target Air Permeability Rate to be achieved.
A temporary air-tight screen is then fitted to an agreed entrance door to the building. A fan is then mounted into the screen and activated to blow air into or out of the building to create a price differential between inside and outside of approximately 50 Pa (Pascals). Up to 7 readings are taken with a no more than 10pa difference. A mean average is taken to establish the buildings leakage rate @ 50pa.
Additionally, both before and after the test, our engineer will take a number of other readings, including barometric pressure, internal/external temperature and wind speed . Through the use of specialist software and the fan in operation, our engineer will be able to fully carry out the test and measure the Air Permeability Rate for the building.
To set up and conduct a single Air Test will take approximately 1 hour, and whilst nobody can be allowed to enter or exit the building during the test itself, tradesmen or contractors can remain working inside throughout the testing process.
What happens after the test is carried out?
Upon completion of the Air Test, our engineer will know whether or not the building has met the required standard for achieving a pass. They will then immediately inform the site contact of the outcome.
Under normal circumstances, the engineer will then upload the respective test results to our in-house systems – the client will then be invoiced the next working day and test reports and certificates issued upon receipt of payment.
By prior arrangement, we are also able to issue test reports and certificates on a same-day basis via email, should the client require immediate access to the results.
What happens if the test fails?
If the Air Test fails to meet the required standard for the Target Air Permeability Rate – our engineer will immediately inform the nominated site contact to discuss his findings and offer to identify areas of concern that may be causing the failure.
Normally, this would take the form of a walk and talk through the building to identify the engineers concerns with a recommended course of remedial action e.g. sealing of gaps between skirting boards and floor.
Often, by agreement, minor areas of concern can be rectified on the day and the engineer will undertake a re-test of the building to see if it will meet the required standard.
Alternatively, ATSPACE will be happy to produce a written report – outlining the areas of concern together with annotated photographs – so that the client can undertake the required remedial action and then book a re-test at a later date.
What about multi-unit testing on large developments?
At ATSPACE, we have extensive experience of conducting Air Pressure Testing on large scale residential developments and we recognise that co-ordinating activities across a large construction site, involving many trades, can often be fraught with problems.
On these larger scale projects, ATSPACE is happy to appoint a dedicated project team – so that you have continuity of contact throughout – and to agree a full testing schedule, in advance, so that both parties know what is to be tested and when. Under these circumstances a single Air Test engineer will be able to carry out up to 15 in a single visit to site.
Our team of BINDT-accredited engineers are fully familiar with all aspects of working alongside construction teams and we guarantee that we will always endeavour to carry out our testing with minimum disruption to the ongoing works on-site, and to complete our testing swiftly, efficiently and through provision of immediate feedback to site representatives regarding testing success or failure.
How can ATSPACE help?
ATSPACE have an experienced in-house team of BINDT-accredited Air Test engineers. We have successfully carried out Air Testing on everything from single dwellings for the home owner to being the preferred Air Testing supplier on some of the largest development sites in the UK.
From initial discussions – regarding: advice and guidance on insulation, provision of air sealing services, pre-test inspections and testing – through to completion of the Air Testing and certification – we will be happy to discuss your requirements and deliver you a first class service with a best price guarantee.
What other services do I need to consider in relation to Air Pressure Testing?
Design stage
Drawing Review / Advice & Guidance
SAP Calculations & PEA
Construction phase
Pre-test Inspections
Contracting Services
As-built stage
Air Tests & Certification
SAP Calculations & EPC
Smoke Testing
What is Sample Testing?
Sample testing is a method whereby testing is carried out on a subset of each dwelling type instead of testing each individual plot. As determined by the Part L1A document, sections 3.17 and 3.18, on each development, an air pressure test should be carried out on three units of each dwelling type or 50%, whichever is less. For the sake of sample testing, blocks of flats are treated as separate developments.
The specific dwellings to be tested should be selected by the BCB in consultation with the pressure tester. The dwellings should be selected so that approximately half of the scheduled tests for each dwelling type are to be carried out during construction of the first 25% of units in that type. The aim of this is to enable any required remedial work, following any failed tests, to be learned and to be adjusted in the design or procedure prior to the majority of the units being completed.
Sample Testing – Pro’s and Con’s
Whilst it might seem like a simple decision to make (less tests = less cost!) unfortunately things are never that simple. Please see below for a list of the pros and cons to sample testing:
Pros
• Providing that all tested plots pass, by achieving a result better than their design air permeability targets, then the fewer tests will mean less cost.
• Having less tests to schedule means that there will be less time delay for the build team to allow for testing.
Cons
• All sample testing results should be notified to the BCB, including details of any failures.
• When your SAP assessor enters your air test results into the SAP software, they must declare whether the result is from testing that specific plot or not. If not, the convention for entering the data is to take the average of all tested results for that dwelling type and add a 2 point ‘penalty’. This means that if the average of results were a score of 3.5, all untested plots would be assumed to score 5.5.
• If a plot fails an air test during sample testing, not only must that plot be retested until it passes, but another plot of the same dwelling type must be tested as well. This can drastically increase both time and financial costs.
• The 2 point ‘penalty’ applied in SAP can also have adverse effects on ventilation strategies. This is because it means that in some cases the figure that needs to be achieved by the tested plots can make a standard System 1 ventilation strategy (intermittent extractors and background ventilation) to air tight. For example, with a design target of 4, the tested plots would need to achieve 2 or under to allow the untested plots to also pass. This would mean that those buildings were too airtight for standard ventilation.
What is a Standard Assessment Procedure (SAP)?
SAP is the UK Government’s Standard Assessment Procedure for energy rating of dwellings. It forms part of the methodology for calculating the energy performance of buildings, and is used to demonstrate compliance with Building Regulations for dwellings – Part L1.
When undertaking the construction of a new building a SAP is normally produced twice during the overall project:
• Design stage SAP – DER & TER Calculations (Dwelling emission Rate & Target Emission Rate) need to be carried out and submitted to local building control before work can commence on the site. If the property is to be sold off-plan a predicted energy assessment (PEA) can be created.
• As-built SAP – is carried out close to completion of the construction project. The completed as-built SAP report will demonstrate that the building meets the compliance standards. An Energy Performance Certificate (EPC) is produced and then lodged with the Landmark database.
What is a Predicted Energy Assessment (PEA)?
A PEA is a Predicted Energy Assessment and is produced as part of the design stage SAP, if required. Many building and construction companies sell properties off-plan – in other words, the builder sells the property to a buyer before the building has been built – and, in order to do so, they must have a valid PEA.
The PEA is also used during the early stages to identify any areas which can be improved to bring the band of the PEA/EPC up if required.
What is an Energy Performance Certificate (EPC)?
An EPC is an Energy Performance Certificate – and shows the energy efficiency and CO₂ emissions for the building on completion of the construction phase and forms part of the as-built SAP. The EPC will also include recommendations on how the property’s energy performance could be improved. It must be issued and lodged with the Landmark database before the property can be signed off and sold.
Prior to issuing the EPC, one element is that a successful Air Leakage Test must have been conducted within the new building and the appropriate Air Test reports and certificates produced along with Part G Water Consumption Calculations to prove regulation standards have been met.
With our own in-house team of fully certified SAP assessors and Air Test engineers – we are able to offer our clients a complete building compliance service from design stage through to completion of the project, including: Air Pressure Testing and Water Calculations/Consumption Certification.
What are the building regulations for SAP, EPC & PEA?
Part L1A of the Building Regulations details the requirements for new build premises and Part L1B covers those requirements that are necessary for conversions and extensions.
When do I need to start planning for SAP/EPC?
In order to comply with the building regulations Part L1, SAP Calculations need to be undertaken on commencement of the design process, during construction and on completion of the build process. This will enable you to take account of and be aware of any changes during the build process that may affect the overall energy rating of the project.
By involving ATSPACE during the early design stages of your project we will produce the required SAP Calculations and PEA (Predicted Energy Assessment) as well as providing advice and guidance on methods of construction and fabrication to ensure that your development achieves the optimum levels of energy efficiency. We will also provide you with the appropriate EPC (Energy Performance Certificate) once the build process has been completed.
How is a SAP rating calculated?
A SAP calculation is a series of calculations, taking into account: space heating, water heating, ventilation and lighting and also taking into consideration potential cost savings generated through the deployment of energy generation technologies e.g. renewables.
Data is collected from a number of sources, including: drawings (floor plans, elevations, site plan, etc.), build specifications, proposed heating and ventilation systems. This information is entered into an accredited software tool to create the draft SAP report. The SAP rating for the building is graded on a scale of 1 to 100 – where 100 represents zero energy costs.
How can I ensure my SAP Calculation is successful?
In simple terms, the earlier you appoint a SAP assessor – the greater your chance of success!
From the plans and drawings provided by the designer during the design stage the assessor inputs the data into approved software – which determines whether the proposed dwelling will comply with the requirements of the building regulations with regards to the conservation of fuel and power. The assessor is able to use the software to model different variations of the design if the initial specification doesn’t show compliance.
The assessor should then advise the designer of the shortfalls and recommend solutions as required. These modifications can then be taken into account, the design revised and appropriate SAP calculations produced for submission to building control.
What happens if I fail my SAP?
In order to achieve compliance with the Building Regulations Part L, it is important to recognise that the production of successful SAP Calculations is part of the overall process, and, in reality you should never begin construction unless you know that you are building to a specification that will meet the requirements.
If your SAP fails at design stage there is little to worry about – as this is a desk based exercise which is carried out before construction commences. The assessor will model different variations of the design if the initial specification doesn’t show compliance – and make recommendations as to alternative ways that the design can be made to meet the requirements.
However, if your SAP fails at as-built stage it may cost a considerable amount of money to fix. You may not have installed sufficient insulation or used the wrong type of heating and ventilation systems during construction – and this, in turn, may require extensive remedial action and / or new systems installed in order to achieve a successful SAP rating.
When will I get my design stage SAP?
Once the SAP Calculation has been produced, our building compliance team will review the report and make recommendations to gain Part L compliance and on how to improve the SAP rating through such things as: improved insulation, different heating systems, etc.
Before issuing the design SAP report the assessor will discuss his recommendations with you, make the agreed amendments and issue the final report which you can then the submit to building control to obtain approval to commence construction.
When will I receive my as-built SAP & EPC?
Prior to issuing the as-built SAP & EPC – a successful Air Leakage Test must have been conducted within the new building. During the design stage for your project, one part of the SAP Calculation will have determined the target Air Permeability Rate (APR) that must be achieved during the final Air Test itself. In essence, the lower the APR, the more stringent you will need to be during the construction phase in minimising air leakage points throughout the building.
At ATSPACE, our building compliance team look at the overall end-to-end process and our SAP assessors and Air Test engineers will always try to ensure that the client has a realistic target to hit come the Air Test day itself. Furthermore, ATPACE offers customers a discounted Air Test fee and the appropriate Air Test reports and certificates produced.
Once the Air Test has been successfully completed, you will be issued with the appropriate as-built SAP and EPC – after which the property can be signed off and sold legally.
How can ATSPACE help?
Here at ATSPACE, we have our own in-house certified On Construction Domestic Energy Assessors (OCDEAs) and we pride ourselves in being able to provide our customers, from home owners to national construction companies, with a professional, experienced and fast turnaround for all aspects of our SAP/EPC service.
In addition to preparing the SAP Calculations, which take into account many factors of energy consumption such as – heating systems, insulation, air tightness, ventilation, lighting and U-value calculations – we also have the building construction skills and expertise to advise on methods of construction and fabrication to ensure that your development achieves the optimum levels of energy efficiency.
What other services do I need to consider in relation to SAP/EPC?
Design Stage
Drawing Review / Advice & Guidance
Construction Phase
Pre-test Inspections
Contracting Services
As-built stage
Air Tests & Certification
Smoke Testing
Water Calcs Part G
Ventilation Part F
Do I need a SAP Assessment for an extension?
Not necessarily – compliance with Building Regulations Part L1B is automatically achieved if:
• The envelope of the extension is sufficiently well insulated
• Glazing is within the extension does not exceed 25% of the floor area
• Building services within the extension are of a sufficient standard.
However when considering an extension, it is advisable to speak with your local building control to determine what level of detail will be required in the SAP Assessment submission.
Do I need a SAP Assessment for a conservatory?
Conservatories and porches are exempt – provided that:
• Conservatory is at ground level
• Floor area is less than 30m²
• Heating system does not extend into the conservatory
• The door and external wall separating the dwelling and conservatory is retained
When should I have my SAP Assessment completed?
In reality, the addition of an extension is likely to change the energy efficiency characteristics of the dwelling and, in order to ensure that you get the design that you want and that it will comply with the Building Regulations, the SAP Assessment for the extension should ideally be completed as soon as the architect or contractor has finalised the proposed build specification.
This way, should the SAP Assessment result in initial compliance failure it will be relatively inexpensive to make amendments to specifications e.g. insulation thickness or material amendments, prior to commencement of any work on the extension.
What if the area of glazing on my extension exceeds 25%?
Let there be light! Modern glass extensions are becoming increasingly popular, yet if the proposed glazing exceeds more than 25% of the extension floor area, additional proof of compliance to Part L of the Building Regulations will be required since glazing and openings lose more heat than walls and roofs.
To demonstrate compliance in these situations involves a 3-stage process:
• Prepare SAP Calculations on the CO₂ emissions for the existing house along with the proposed extension.
• Calculate the CO₂ emissions for the existing house with a ‘notional extension’. A notional extension is an extension that meets the minimum standards of Part L1B of the Building Regulations
• Compliance is achieved provided the proposed CO₂ emissions are less than the notional CO₂ emissions
These are known as ‘trade-offs’ and can include exceeding the minimum thermal standards elsewhere within the extension. Examples of commonly recommended improvements include additional depths of insulation to the extension floor or roof, improved glazing specifications, top up loft insulation or cavity wall insulation to the existing property, or improvements to the existing heating system.
What information will be required to carry the SAP Assessment?
Under normal circumstances, preparing a SAP Assessment is a desk-based exercise and all the calculations will be drawn from a completed SAP Assessment checklist, including:
• Floor plans and drawings
• Details of the building’s location and orientation
• Specification for the construction of all floors, roofs and external walls
• Specification for all windows and doors within the buildings external envelope
• Details of the primary heating system e.g boiler make / model
• Details of the hot water system and insulation of cylinder and pipes
• Details of any fixed secondary heating e.g wood burning stove
• The number of standard light bulbs and the number of low energy light bulbs
• Details of any renewable technology – e.g. solar hot water or photovoltaics.
How can ATSPACE help?
Here at ATSPACE, we have our own in-house certified On Construction Domestic Energy Assessors (OCDEAs) and we pride ourselves in being able to provide our customers, from home owners to national construction companies, with a professional, experienced and fast turnaround for all aspects of our SAP/EPC service.
In addition to preparing the SAP Calculations, which take into account many factors of energy consumption such as heating systems, insulation, air tightness, ventilation, lighting and U-value calculations – we also have the building construction skills and expertise to advise on methods of construction and fabrication to ensure that your development achieves the optimum levels of energy efficiency.
Do I need a SAP Assessment for a conversion?
SAP Calculations are required for all buildings converted to new dwellings e.g. flat conversions and barn conversions in order to demonstrate compliance with Part L1B of the Building Regulations.
The SAP Assessment process calculates the thermal efficiency of the proposed building fabric including any upgrades that may be made, together with the energy requirements of the proposed heating, lighting and hot water systems of the planned property.
Unlike SAP for new build, conversions do not currently have to demonstrate compliance with any prescribed limits on CO₂ emissions.
When should I have my SAP Assessment completed?
If you are undertaking a conversion of an existing building, the initial SAP Calculations must be prepared at design stage for the property and submitted to local building control before any development work commences.
Once the conversion works have been completed an as-built SAP Calculation is prepared and will incorporate any design changes that have occurred along with the finalised details regarding heating, hot water and ventilation systems that have been installed.
The finalised SAP Reports are then produced for submission to building control together with an On Construction Energy Performance Certificate (EPC) which is required by building control prior to the issue of the completion certificate and also for the subsequent sale or let of the property.
What are SBEM Calculations?
SBEM Calculations (Simplified Building Energy Model) are a requirement of the Building Regulations Part L2 and must be submitted to building control at two stages in the development process:
• Design stage – prior to commencement of the development project, an SBEM Calculation must be submitted to your local building control, alongside your application
• As-built stage – upon completion of the building phase, it is required that both an SBEM Calculation and an EPC are submitted prior to sign-off by Building Control
SBEM is an approved software tool that is used to calculate the monthly energy consumption for: space heating and cooling, water heating, ventilation and lighting, and also estimates the annual total of CO₂ emissions for the building.
What is an Energy Performance Certificate (EPC)?
An EPC is an Energy Performance Certificate and shows the energy efficiency & CO₂ emissions for the building on completion of the construction phase.
The EPC must be issued before the property can be sold and forms part of the as-built SBEM which is calculated after a successful Air Leakage Test has been conducted within the new building and the appropriate Air Test reports and certificates produced.
Additionally, for commercial buildings open for public use and over 500m² we are able to supply you with the appropriate energy certificate which must be publicly displayed within the building showing an A-G Rating based on energy performance and CO₂ emissions.
What are the Regulations regarding SBEM/EPC?
Part L2A of the Building Regulations details the requirements for new build commercial premises and Part L2B covers those requirements that are necessary for conversions and extensions.
Part L2 of the Building Regulations dictates that five separate criteria should be met with some of the criteria being interdependent with each other:
1. Achieving an acceptable building CO₂ emission rate
2. Limits on design flexibility
3. Limiting the effects of solar gains in summer
4. Quality of construction and commissioning
5. Providing information (for the building operator)
What is the driving force behind these regulations?
Energy consumption within non-domestic buildings accounts for approximately 18% of CO₂ emissions across the UK. Part L2A of the Building Regulations (revised in 2006) stipulated an improvement rate of between 23.5% and 28%, above the 2002 standards, for the energy performance of new buildings – included in this was a 10% contribution from Low/Zero Carbon Technologies (LZC) to help meet these targets.
As the UK government has a long-term goal of achieving a 60% reduction in UK CO₂ emissions by 2050, it is expected that the Building Regulation Part L will enforce even more stringent standards over time. Some Councils have already introduced their own standards which require the incorporation of LZC technologies into new buildings.
When do I need to carry out SBEM Calculations?
In simple terms – without an SBEM Calculation you cannot begin the construction project!
SBEM Calculations (Simplified Building Energy Model) are a requirement of the Building Regulations Part L2 and must be submitted to building control at two stages in the development process:
• Design stage – Prior to commencement of the development project, an SBEM Calculation must be submitted to your local building control, alongside your application
• As-built stage – Upon completion of the building phase, it is required that both an SBEM Calculation and an EPC are submitted prior to sign-off by building control.
Our Assessors normally begin the process during discussions with developers, architects and designers – often playing a key role in helping our clients to reduce long-term energy costs – because of their skills and expertise of being able to recommend optimum levels of insulation and assessing the benefits of more efficient building services.
In helping our customers through the SBEM process we will be happy to undertake on-site visits, carry out measured surveys and execute the required level of Air Leakage Testing, Smoke Testing and Thermography prior to preparation of the final SBEM Reports and their subsequent filing on the Landmark database.
How is SBEM Calculated?
SBEM is used to create models and simulations of the proposed building, when compared against a notional building of the same dimensions and functionality, via the National Calculation Method Database. An improvement factor is then applied to establish a Target Emission Rate (TER) against which the actual design Building Emission Rate (BER) must equal or better.
The majority of this work is a desk-based exercise utilising approved software. The start point for the creation of SBEM calculations is for one of our certified SBEM assessors to review the detailed plans, drawings and specifications, including building fabric and mechanical and electrical installations, and to prepare the formal SBEM Report for submission to building control.
How can ATSPACE help?
At ATSPACE, our fully qualified assessors follow an established process for providing – advice, guidance and support, from design stage through to submission of the final reports that must be uploaded to the Landmark Database, once the as-built stage has been fully assessed.
Our aim, at ATSPACE, is to help our customers every step of the way and we have every confidence that our team of skilled, experienced & certified assessors and engineers can help you achieve building compliance success through each phase of your project.
What other services do I need to consider in relation to SBEM?
Design stage
Drawing Review / Advice and Guidance
BREEAM Assessment
Construction phase
On-Site Measuring Surveys
BREEAM Assessment
Contracting Services
As-built stage
Air Pressure Tests and Certification
BREEAM Assessment
Smoke Testing and Thermography
What is Sound Insulation Testing all about?
Sound insulation provides resistance to the passage of sound through walls and floors and within a building – sound is categorised as either ‘airborne’ (through talking, or home entertainment systems) or ‘impact’ (generated through an impact striking on the floor e.g footsteps).
Sound Insulation Testing is the methodology used to quantify the resistance to the passage of sound through the walls and floors of adjoining buildings e.g. between adjoining walls of a pair of semi-detached houses; through the floor linking an upstairs flat to the commercial office below or through the wall of adjoining hotel rooms.
What are the regulations for Sound Insulation Testing?
Unless built under the Robust Details Scheme, the UK Building Regulations require Pre-Completion Sound Insulation Tests to be carried out in all new-build dwellings and conversions that involve two adjoining dwellings with separating partition walls or floors, in order to comply with Part E of the Building Regulations.
What is the Robust Details Scheme?
New builds that have been constructed under the Robust Details Scheme do not have to undertake pre-completion sound insulation testing in order to satisfy Part E of the Building Regulations.
A robust detail is a separating wall or floor construction that has been registered, approved and assessed by Robust Details Ltd. (RDL). Full details are to be found in the RDL Handbook and each plot needs to be formally registered with RDL, who will carry out on-site inspections during the build process to check that the plots are complying with the standards of the scheme.
How much Sound Insulation Testing is required?
On larger construction sites, where there is a mix of dwelling types (e.g. 3 bed Semi-Detached, 2 Bed Flats, etc.) – Part E of the Building Regulations Section 1.30 states:
Building control bodies should stipulate at least one set of tests for every ten dwelling – houses, flats or rooms for residential purposes in a group or sub-group.
If you are at all unsure of how many tests to budget for please give ATSPACE a call and one of our ATTMA-Accredited Engineers will be happy to talk you through the process and provide advice upon the overall number of tests that may be required.
However, given the complexity of mixed dwelling type development projects, which involve differing designs and fabrication please contact your local building control who will confirm the total number of tests that will be required by dwelling type across the whole site.
When should I carry out my Sound Insulation Test?
The Sound Insulation Test is carried out after the second-fix stage. The following checklist, prior to testing needs to have been completed:
• Windows and external doors need to have been installed, glazed and closable
• Window trickle vents should be installed and closed (or temporarily blocked for testing)
• All internal doors should be in place and hung
• Power, TV/satellite and power sockets should be fitted and in place
• All wall surfaces in rooms to be tested must be completed
• Floors and ceiling surfaces are completed
• Cornices and skirting boards are in place
• Ideally carpets should not have been fitted in rooms to be tested (however – if carpet has been glued to the floor the regulations permit the use of a board placed on the carpet for impact testing)
• Where laminates and vinyl form part of the standard construction – testing can be carried out with these in place.
• Rooms to be tested should be clean and tidy
• No other trades should be working in the dwelling during the test
• Access will be required to the properties on both sides of the floor/walls to be tested
• 240v power is live (110V is allowable by prior arrangement)
Additionally, if you are unsure about any aspects of the sound insulation process prior to testing, ATSPACE will be happy to provide you with a design review – to review drawings and advise on appropriate sound insulation methods.
What does the Sound Insulation Test entail?
There are two main types of Sound Insulation Test:
• Airborne Test (to BS EN ISO 140-4)
This type of test measures the resistance to the passage of airborne sound through separating walls or floors. This is carried out by the test engineer using a high power multidirectional loudspeaker which creates steady levels of noise which are measured at differing locations in both the source and receiving rooms. Such tests can take place vertically (through party floor) or horizontally (through party wall).
• Impact Test (to BS EN ISO 140-7)
A tapping machine, which generates impact sound, is used to measure the passage of sound through the floor insulation to the room directly below. With an Impact Test, it is important that it is conducted directly onto the bare floor and before the fitting of any carpets or other floor covering.
The Sound Insulation Test is carried out according to a strict code of conduct and whilst our Sound Test engineer will be happy to outline the process to you – he must be left alone whilst conducting the formal test itself.
What is involved and what site conditions are needed for the Sound Test to be carried out?
What is involved
• The test is carried out between a pair of rooms separated by a party wall or floor.
• It involves setting up a noise source in the room on one side of the party wall or floor and measuring this noise on the other side of the partition.
• We will require simultaneous access to both sides of the wall or floor
• In the interest of health and safety, we cannot allow anyone in the room that we are testing to or from as the equipment emits a sound over 100 Db.
Required site conditions
• Quiet conditions will be required – with no work at all near the rooms in question.
• Staff should be informed of the Sound Testing programme and be prepared to leave punctually as required.
• External noisy activity within control of the site manager should be stopped.
• ATSPACE should also be informed of any other noisy activity likely to be occurring on the test day e.g.roadworks.
• The tests are likely to last several hours – depending on the number of tests involved.
What happens after my Sound Insulation Test?
Upon completion of the required Sound Insulation Testing our Engineer will upload all test data to the ATTMA Portal, from which ATTMA-approved Sound Insulation Reports are downloaded and then forwarded to you, via email, for subsequent submission to building control. Once created, all formal Reports may be accessed directly from the ATTMA Portal by keying in the relevant Job Reference and Site Post Code.
How can ATSPACE help?
With our own in-house team of ATTMA-Accredited Acoustics Engineers we are regularly asked to undertake much more than Pre-Completion Sound Insulation Testing and we are happy to provide support in a wide variety of circumstances that require fully accredited acoustics and noise expertise, including:
• Design and drawings reviews – regarding sound insulation options and
• Noise impact assessment – Construction sites, housing developments and environmental
• Acoustic design and testing – BB93 for Schools
• Noise impact assessment – Entertainment events e.g. pubs, clubs, outdoor events
• Provision of acoustic evidence e.g. public inquiries, planning authorities and licensing committees
What other services do I need to consider in relation to Sound Insulation Testing?
Design stage
Drawing Review / Advice and Guidance
SAP Calculations & PEA
Construction phase
Pre-test Inspections
Contracting Services
As-built stage
Air Tests & Certification
SAP Calculations & EPC
Smoke Testing
What is Thermography and Thermal Imaging?
Thermal Imaging Services provide the most effective (and only!) visual aid technology to enable identification of any problematic heat loss areas within the external and internal envelope for ALL types of buildings.
Thermography is the name for a type of photography which is based on infrared wavelengths – whilst conventional photography relies on reflected energy from a light source, which is visible to our eyes.
Thermography is used to identify areas of inadequate insulation, air leakage paths and thermal bridges that may need to be addressed to comply with Building Regulations – Part L for new buildings or to reduce heating costs for existing buildings.
Why use Thermal Imaging?
Carrying out building inspections, using a thermal imaging camera is a powerful and non-invasive means of diagnosing the condition of buildings and identifying problem areas – allowing them to be photographed, documented and corrective action put in place before becoming more serious and more costly to repair.
Because a thermal imaging camera can see the ‘invisible’, the thermographic technician can quickly identify problem areas – photograph and record the data for reporting – because a thermal imaging camera will give you a total view of the situation and instant diagnostic insights.
What are the benefits of Thermography?
Thermal imaging cameras are the perfect tool for locating and identifying areas of poor insulation or construction – because through infra-red imaging we are able to see that which is normally invisible!
A thermal imaging camera will record accurate temperature data and produce images that provide building personnel with instant information regarding a wide range of potential problem areas, including:
• Detect poor/missing Insulation
• Locate water ingress in flat roofs
• Identify source of air leaks
• Identify electrical faults
• Find moisture in roofs and walls
• Detect mould
• Locate thermal bridges
• Detect construction weaknesses
Thermal imaging is the most rapid and non-invasive way of identifying areas of heat loss within a building. The surveys can also identify areas for potential improvement, minimising energy wastage and reducing running costs and CO₂ emissions.
When is a Thermographic Survey carried out?
Thermographic Surveys are usually conducted around second-fix stage and can quickly identify problem areas inherent in the building construction and fabrication.
Surveys are normally carried out at night or early morning, when environmental conditions are suitable and the effects of solar loading effects have disappeared. Also, it is important that there is at least a 10°C difference between internal and external temperatures of the building, which means heating systems should have been in operation for at least 8 hours prior to the survey.
What happens during a Thermographic Survey?
Thermal imaging cameras are the perfect tool for locating and identifying building failures because on the thermal image – problems seem to jump right out at you.
The thermographic engineers will normally take both conventional and thermal images of each elevation of the building from the outside. These images are then reviewed and if anomalies are identified the building would be further scanned from the inside and images and analysis recorded.
Subsequently, a detailed report would be produced identifying any issues or problem areas in order to make recommendations for remedial action.
Can a Thermographic Survey help with BREEAM?
A commitment to and evidence of a Thermographic Survey can generate credits as part of the BREEAM scheme, provided the survey is carried out by a Level 2 PCN Certified Thermographer.
How can I avoid failing a Thermographic Survey?
Detailed Thermographic Surveys can be provided on completion of the build process, or even during, to highlight any thermal anomalies and inconsistencies in the envelope caused by air leakage or by damaged or missing insulation.
Given that thermal imaging ‘sees everything’ it is important that maximising energy efficiency is built-in to both design and construction phases of the project. That way, once the building envelope is complete, thermal imaging can be used as a form of quality assurance to ensure that anomalies and air leakage problems are addressed along the way.
How can ATSPACE help?
Alongside our extremely price-competitive and extensive Air Pressure Testing services, we are also able to offer customers Thermographic Surveys and Thermal Imaging Services – which provide our residential and commercial customers with a full belt and braces service to help you maximise energy efficiency within your building.
Detailed Thermographic Surveys can be provided on completion of the build process, or even during, to highlight any thermal anomalies and inconsistencies in the envelope caused by air leakage or by damaged or missing insulation. All surveys are carried out in accordance with BRE 176 by an accredited thermographic engineer.
What other services do I need to consider in relation to Thermography?
Design Stage
Drawing Review/Advice and Guidance
Construction Phase
Pre-test Inspections
Contracting Services
As-built Stage
Residential Air Testing
Commercial Air Testing
Smoke Testing
What is Ventilation Testing Part F all about?
The Building Regulations L1A & L1B require that buildings are designed to be more air tight, thereby reducing CO₂ emissions and becoming more energy efficient. However, this removes a source of ventilation and if the installed ventilation system is not operating efficiently, then the building could attract damp and condensation issues, especially during prolonged periods where the windows are kept closed.
Part F of the Building Regulations introduced more stringent ventilation requirements for buildings and it is of equal importance that any installed ventilation systems are fit for purpose, balanced and commissioned correctly to ensure optimum levels of operation. Additionally, the regulations also state “there shall be adequate means of ventilation provided for people in the building”.
Part F of the Building Regulations requires that MHVR Systems (Mechanical Ventilation and Heat Recovery) and intermittent extractor fans (e.g. kitchen & bathroom) have their flow rates checked, are working efficiently and the relevant test results submitted to building control as part of the overall building compliance process.
What is the aim of the Regulations for Ventilation Part F?
In October 2010, Part F of the Building Regulations was issued and this placed an increased emphasis around the requirement for effective design, installation and operation of ventilation systems.
The overall aim of the regulations is to maximise CO₂ reduction through optimally designed systems, competent system installation and verification of performance once the system has been installed and in operation by the home owner.
In order to provide additional advice and guidance on how to conform to the revised regulations of October 2010, the Domestic Ventilation Compliance Guide was also introduced. Download your copy.
What Ventilation Systems are covered in the Regulations for Ventilation Part F?
There are 4 types of ventilation system covered by the Buildings Regulations:
• SYSTEM 1 – Intermittent fans e.g. extract fans and background ventilation e.g. trickle vents
• SYSTEM 2 – Passive stack – which provides natural ventilation e.g. chimney. Testing is not required for this type of system
• SYSTEM 3 – Continuous mechanical extract ventilation (MEV). Typically, these are continuously operating extract fans that are installed in kitchens and bathrooms
• SYSTEM 4 – Continuous mechanical balanced ventilation with heat recovery.
The performance rates for each system type detailed in Part F are the minimum requirements necessary to ensure that adequate air quality is provided for the occupants indoors. The occupant’s health could be at risk if these ventilation rates are compromised.
Under normal circumstances, we are able to carry out Part F testing alongside our on-site Air Pressure Test, thereby enabling you to achieve both Part L and Part F compliance in the most time-efficient, cost-effective manner.
When is the Part F testing carried out?
The Part F Ventilation Testing is carried out once the building has been completed. The building does not need to be decorated or have floor coverings fitted however all aspects of the ventilation system should have been commissioned and fully operational.
All Part F testing is carried out by one of our BPEC accredited engineers, using UKAS calibrated equipment. We will require the following:
• For each dwelling to be tested, a list of fan manufacturers, model numbers and installation location
• All fans to be tested must be installed and operational
• All trickle vents must be installed and set in the open position
• All windows and doors to be fitted and set in the closed position
What does the test entail?
Using UKAS calibrated equipment, our BPEC accredited engineers measure the air flow rate for each individual component of the ventilation system e.g. cooker hoods and extraction fans.
Overall, testing is a simple process, with each test only lasting a few minutes. The engineer will measure and record the air flow rates for each component using an anemometer which generates the readings.
Upon successful completion of the testing, our BPEC accredited engineer will provide the appropriate certification for submission to your local building control.
How can ATSPACE help?
ATSPACE have an experienced, in-house team of BINDT & BPEC accredited test engineers. We have successfully carried out Part F Ventilation Testing on all types of ventilation systems across the UK.
When combined with our Part L Air Testing Service, we are able to carry out your Part F Ventilation Test in a single on-site visit – saving you money.
What other services do I need to consider in relation to Part F Ventilation Testing?
Design Stage
Drawing Review/Advice & Guidance
SAP Calculations & PEA
Construction Phase
Pre-test Inspections
Contracting Services
As-built Stage
Air Permeability Tests & Certification
SAP Calculations & EPC
Smoke Testing
What is Water Efficiency Part G of the Building Regulations?
The Code for Sustainable Homes was introduced in 2007 and Part G of the Building Regulations now includes water efficiency for the first time. In addition, improved water efficiency in new developments will be backed-up through the planning system, as the Government allows the planning system to mandate water efficiency targets in excess of the Building Regulations where there is demonstrable local need.
If you are building a new home, you must ensure that it will have a predicted water consumption of less than 125 litres per person per day.
What is the Water Efficiency Calculator for new homes?
The Water Efficiency Calculator for new dwellings is the Government’s national calculation methodology for assessing water efficiency in new dwellings in support of The Code for Sustainable Homes and the Building Regulations.
If you are building a new home you will need to use the methodology outlined in this document to calculate the water consumption of the dwelling. This is calculated using a number of assumptions outlined in the guidance and is calculated in litres per person per day.
What water consumption levels are required for Code for Sustainable Homes?
Introduced in 2007, the Code for Sustainable Homes is the Government’s main tool for improving the environmental specification of new homes. Points are awarded for achieving set standards in 9 different aspects of development.
Water consumption inside the home is one of the compulsory aspects to address to achieve minimum standards at levels 1-6 of the code. Daily consumption of water is calculated using the water efficiency calculator for new dwellings, as detailed in the Code for Sustainable Homes technical guidance. A total of 5 credits are available for water consumption. The water consumption specification for increasing code levels are:
When do I actually have to complete the Water Calculator?
The Water Calculator will be completed initially when fittings and appliances are specified during the design stage of the project and then revised if those fittings subsequently change during the construction and fitting out stage. The regulations require only that the notice states the potential consumption, however, at ATSPACE we prepare you a detailed report enabling you to submit a completed copy of the calculations to Building Control.
Can I use the results from the calculator in a planning application?
Yes you can – provided you have the calculation results verified and approved by a Building Control officer or suitably qualified Code for Sustainable Homes assessor.
Here at ATSPACE, we often carry out Water Efficiency Calculations for clients alongside the preparation of the SAP / EPC Assessment. In doing so we would enter all the details into approved software to produce a detailed report ready for submission to Building Control at both design stage and as-built stage.
What can I do to decrease water usage?
Achieving greater levels of water efficiency is often more about reducing the amount of water that is wasted – rather than by restricting use. This can be achieved by making small behavioural changes, choosing water efficient products and by recycling water. Ways of reducing the amount of water wasted in the home and garden can include:
• Using dual flush toilets as intended and using full flush only when needed
• Having showers rather than baths
• Install water efficient washing machines and dishwashers
• Use a watering can rather than a hose or sprinkler in the garden
• Collect rainwater in a water butt to irrigate the garden
• Repair leaks and dripping taps as soon as possible
How can I ensure I meet the standard required for Water Efficiency?
To achieve Level 0 of the Building Regulations, which is using less than 125 litres per day per person, is not an arduous task. However, water efficiency is an important part of the Code for Sustainable Homes and water efficient products (fittings, appliances and systems) can use significantly less water than conventional products.
When designing your new build property, it is important to take projected water usage into account and consider some the water efficient products that are on the market today, including:
• Low-flow taps
• Low water use washing machines
• Low volume flush WCs
• Low water use dishwashers
• Reduced volume baths
• Rainwater harvesting systems
• Low-flow showers
• Greywater recycling systems
If you would like to know more about Part G Water Efficiency and how to go about preparing the Water Efficiency Calculations – please call ATSPACE, one of our assessors will be happy to talk you through the process, or alternatively download the water efficiency in new homes guide which provides house builders with a comprehensive insight into achieving water efficiency.
What does the Water Calculations entail?
As part of Water Efficiency Calculations we will ask you to complete a checklist which identifies all the fixtures and fittings that will be using water. To find the information about your fittings, look first at the paperwork that comes with the fitting, or if it is not there ask your builder, plumber or supplier, alternatively you can look on-line by typing in the fitting name and manufacturer.
The majority of the details required are – the make and model number of the equipment or fitting being installed, along with any floor plan you have for the property. All the relevant data is entered into approved software and we then provide you with a detailed report – which shows the projected water usage for the property. This report can then be submitted to Building Control.
Where can I find information on fittings in order to complete the water efficiency calculation?
The details required for Water Efficiency Calculations can be found in the following:
• Paperwork provided with fixtures and fittings e.g. showers, taps
• Manufacturers’ handbooks for electrical appliances e.g. dishwashers, washing machines
• Manufacturers’ websites
How can ATSPACE help?
At ATSPACE, we pride ourselves on offering our clients a full building compliance service, including: Initial advice and guidance; SAP/EPC Calculations and Air Leakage Testing. We will happily undertake Water Efficiency Calculations on behalf of your development project.
What other services do I need to consider in relation to Part G Water Efficiency?
Design Stage
Drawing Review / Advice & Guidance
SAP Calculations & PEA
Construction Phase
Pre-test Inspections
Contracting Services
As-built Stage
Air Tests & Certification
SAP Calculations & EPC
Smoke Testing
What are our Terms and Conditions?
Please read our Terms and Conditions here.
What is our VAT treatment on our services provided?
Please read our Terms and Conditions here.